What is the most common backflow prevention device?
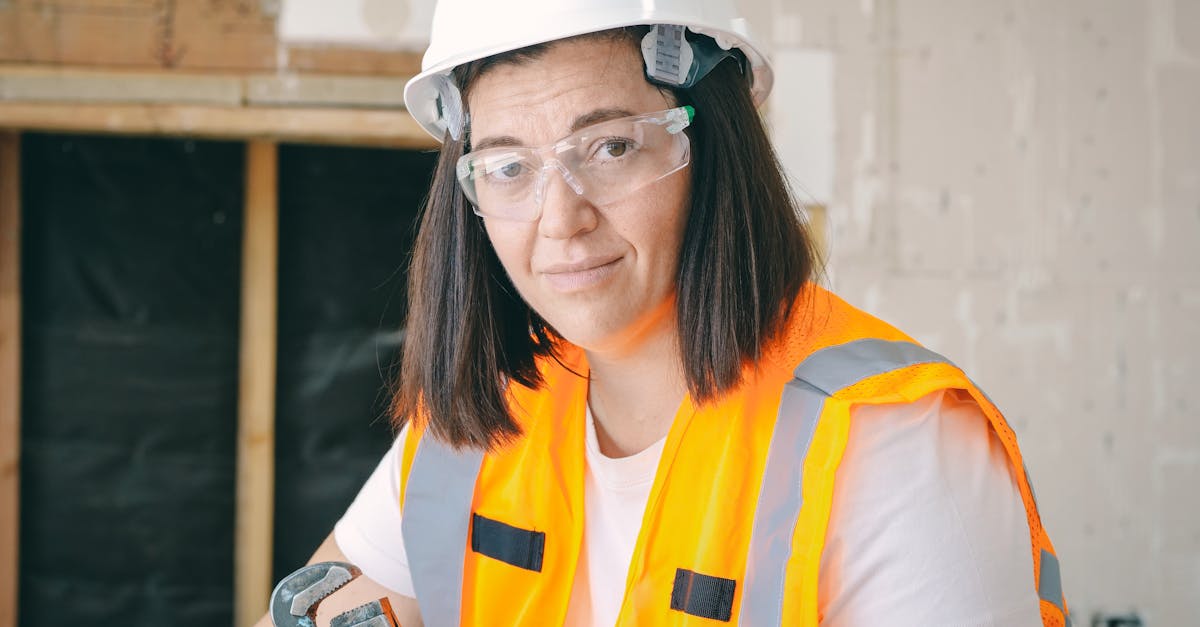
Table Of Contents
Regulations and Standards for Backflow Prevention
Regulations and standards governing the installation and maintenance of backflow prevention devices are crucial to ensure the safety of water supplies. In Australia, backflow prevention is highly regulated by state and territory legislation. These regulations require property owners to conduct regular tests and inspections of backflow prevention devices to mitigate the risk of water contamination. Failure to comply with these standards can result in penalties and fines, emphasizing the importance of adhering to regulatory requirements.
The Australian Standard AS/NZS 2845 provides comprehensive guidelines for the selection, installation, testing, and maintenance of backflow prevention devices. This standard outlines the minimum requirements for protecting potable water supplies from contamination due to backflow incidents. Adhering to AS/NZS 2845 ensures that backflow prevention devices are installed correctly and function effectively, safeguarding public health and the integrity of the water supply system. Compliance with these regulations is essential to maintain the quality and safety of water resources in Australia.
Compliance Requirements for Backflow Prevention Devices
Compliance requirements for backflow prevention devices in Australia are stringent to ensure the safety of potable water systems. These devices are crucial in safeguarding against the contamination of water sources by preventing the unwanted flow of potentially harmful substances back into the water supply. Local regulations and standards mandate the installation of backflow prevention devices in specific settings to mitigate the risks associated with cross-connections. These regulations outline the types of backflow prevention devices that must be installed based on the level of hazard present and the potential consequences of backflow incidents.
In Australia, backflow prevention devices must be tested and maintained regularly to ensure their effectiveness in preventing backflow incidents. Regular inspections by certified professionals are necessary to verify that the devices are functioning correctly and are in compliance with regulatory requirements. Failure to adhere to these compliance requirements can result in severe penalties and jeopardise the safety of the water supply. It is essential for property owners and managers to understand and implement the necessary measures to maintain backflow prevention devices in optimal condition to protect public health and comply with regulatory standards.
How Backflow Prevention Devices Work
Backflow prevention devices play a critical role in safeguarding potable water systems against potential contamination. These devices work by ensuring that water flows in a single direction, preventing any reverse flow or backflow of harmful substances into the clean water supply. In the event of a change in pressure within the plumbing system, backflow prevention devices act as barriers to stop contaminated water from entering the main water supply, thus maintaining the integrity and safety of the water distribution network.
There are various mechanisms employed by backflow prevention devices to achieve this critical function. One common approach involves the use of check valves that allow water to flow in one direction while blocking any reverse flow. Additionally, some backflow prevention devices utilise air gaps, which create a physical space between the water outlet and potential contaminants, ensuring that no backflow can occur. By employing these different mechanisms, backflow prevention devices effectively mitigate the risk of contamination in water systems, promoting public health and safety.
Mechanisms of Backflow Prevention
Backflow prevention devices are essential components of plumbing systems, ensuring the purity of water supply by preventing contaminants from flowing back into the mains. These devices operate based on various mechanisms that collectively serve to maintain the integrity of the potable water supply. One common mechanism involves the use of check valves, which allow water to flow in only one direction, effectively blocking any reverse flow that could potentially cause contamination. In addition, air gaps provide a physical break between the water sources, creating a space that prevents backflow in the event of a drop in pressure or siphonage.
Moreover, backflow prevention devices may incorporate reduced pressure zones (RPZ) or pressure vacuum breakers (PVB) to safeguard against backflow incidents. RPZ devices employ a series of check valves and an intermediate zone of reduced pressure to ensure that contaminated water cannot enter the clean water supply. On the other hand, PVB devices feature a spring-loaded check valve that closes once water flow stops, preventing any reverse flow. Understanding the various mechanisms of backflow prevention is crucial for maintaining the safety and quality of water systems to protect public health.
Cost Analysis of Backflow Prevention Devices
Backflow prevention devices are essential for ensuring the safety of water supply systems by preventing contaminated water from flowing back into clean water sources. When considering the cost analysis of backflow prevention devices, it is crucial to assess the initial investment along with long-term maintenance expenses. The pricing of these devices can vary depending on the type of backflow prevention system required for a specific environment, such as residential, commercial, or industrial settings.
Factors influencing the cost of backflow prevention devices include installation charges, annual testing fees, repair and replacement costs, as well as compliance expenses with local regulations. As part of a comprehensive cost analysis, it is important to also consider the potential savings associated with preventing water contamination incidents and avoiding fines due to non-compliance with backflow prevention regulations. Investing in reliable backflow prevention devices can contribute to safeguarding public health and ensuring the integrity of water supply systems.
Budgeting for Backflow Prevention Systems
When budgeting for backflow prevention systems, it is essential to consider both the initial costs of the devices and the ongoing maintenance expenses. The cost of backflow prevention devices can vary depending on the type of system needed and the size of the property. It is advisable to research different options to find a solution that meets regulatory requirements while staying within budget constraints. Additionally, factoring in the cost of installation by a certified professional is crucial to ensure the system is properly set up to prevent any backflow incidents.
Besides the expenses related to purchasing and installing backflow prevention devices, it is important to allocate funds for regular inspections and maintenance. Routine check-ups by qualified technicians help to guarantee that the system is operating correctly and remains compliant with regulations. By including these costs in the budget for backflow prevention systems, property owners can ensure the continuous functionality of their backflow prevention devices and mitigate the risk of contamination incidents.
FAQS
What is the most common backflow prevention device?
The most common backflow prevention device is the double check valve (DCV) assembly.
How does a double check valve (DCV) assembly work?
A double check valve (DCV) assembly works by using two check valves to prevent backflow of water, ensuring water only flows in one direction.
Are double check valve (DCV) assemblies compliant with regulations and standards for backflow prevention?
Yes, double check valve (DCV) assemblies are commonly used and are compliant with most regulations and standards for backflow prevention.
What are the costs associated with installing a double check valve (DCV) assembly?
The cost of installing a double check valve (DCV) assembly can vary depending on various factors such as size, location, and installation requirements. It is recommended to consult with a professional for a cost analysis.
How frequently should double check valve (DCV) assemblies be tested and maintained?
Double check valve (DCV) assemblies should be tested and maintained annually to ensure they are functioning properly and in compliance with regulations. It is important to schedule regular maintenance to prevent backflow incidents.
Related Links
Backflow preventionHow do I know if I have a backflow prevention device?
What is the backflow prevention?
What is the Australian standard for backflow prevention?
How can you prevent backflow?
Why is a backflow prevention device required?
What is the reason for a backflow?
What is the only safe method for backflow prevention?
What is a backflow to keep the water supply safe?
What happens if you don't have a backflow preventer?
What is the only 100% way to prevent backflow?
What is the most reliable method for preventing backflow?
What device is used to prevent a backflow?
What does a backflow device look like?
Does every house have a backflow valve?
How to prevent backflow in plumbing?
How does backflow prevention work?
What is the purpose of a backflow preventer in a plumbing system?
How to fix plumbing backflow?
How do I stop my plumbing from backing up?
How do I know if my house has a backflow preventer?
What is the only completely reliable backflow prevention device?
Which plumbing device helps prevent a backflow?
Do I really need a backflow preventer?
Why would you need to prevent backflow?
What is another name for a backflow preventer?
What is the most effective type of backflow prevention?
Which method will prevent backflow?
How does a backflow system work?
What equipment requires a backflow preventer?